Supplementary Cementitios Materials to Enhance Durbility of Concrete Bridge Decks
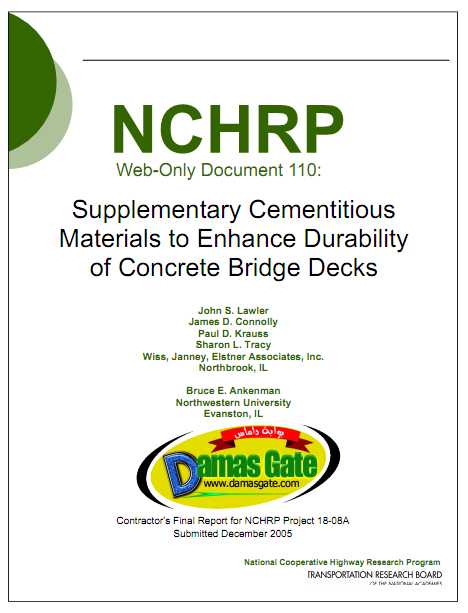
INTRODUCTION AND RESEARCH APPROACH Problem Statement
Premature deterioration of our nation’s concrete bridges has been a persistent and frustrating problem to those responsible for maintaining those bridges as well as to the traveling public. The deterioration typically consists of concrete delamination and spalling due to various mechanisms, including corrosion of embedded steel reinforcement, repeated freezing and thawing, deicing salt-induced scaling, or reactive aggregates. The rate of these mechanisms is primarily dependent on the resistance of the concrete to the ingress of moisture and aggressive substances and on cracking of the concrete.
cracking of the concrete. Since nearly all concrete deterioration processes are driven in some manner by the ingress of water and water-borne agents, such as chloride and sulfate ions, one way to minimize these problems is to make the concrete less permeable. Concrete is primarily made less permeable by densifying the cementitious paste. This is achieved by lowering the water-cementitious materials ratio (w/cm) and by adding supplementary cementitious materials (SCMs), such as silica fume, fly ash, ground granulated blast furnace slag, or metakaolin. However, regardless of how impermeable the concrete cover is, if the concrete cracks, aggressive agents may reach the interior of the concrete and the reinforcing steel and promote deterioration.
Excessive cracking can result from freezing and thawing action, alkali/silica reactions (ASR), corrosion of reinforcement, plastic shrinkage, restrained drying shrinkage, or thermal stress. Early-age cracking became relatively common within the past 30 years as practitioners strived to use less permeable concrete made with extremely low w/cm and high dosages of some SCMs, such as silica fume. These mixtures often produced very high-strength concrete that was prone to thermal, drying, and plastic shrinkage cracking. As these problems have surfaced, researchers and practitioners have developed materials, mixtures, and construction practices to combat these problems and prolong the life of concrete in bridges. It is now better understood that to make durable concrete, high strengths are not necessarily required. High strengths may in fact be detrimental due to the concomitant high modulus of elasticity and low creep, which can result in the development of restraint-induced stresses sufficient to produce cracks. Instead, the mixture performance can be balanced to minimize permeability and shrinkage/thermal cracking while enabling ease of placement, consolidation, and finishing.
The use of SCMs, such as fly ash, silica fume, slag, and natural pozzolans, in concrete bridge decks has become a widely accepted practice by many state highway agencies seeking to maximize durability. This practice is justified by a great deal of research that has been performed on properties of concrete containing one or more supplementary cementitious materials. However, this prior research, necessarily conducted on individual SCM sources, has not provided clear nor universally applicable conclusions concerning the optimum use of these materials. A “one size fits all” approach to concrete mixtures does not achieve the goal of maximizing long-term durability. This is because the quality of local materials used to produce the concrete strongly influences mixture properties and performance. There are large variabilities within, and interactions between, concrete raw materials, and these influence the short-term properties and long-term durability of the concrete. In addition, service environments and the associated deterioration mechanisms vary with geographical location. As a result, concrete mixtures cannot be truly optimized without direct testing of local materials and evaluating the concrete produced with those materials relative to local performance demands. Therefore, research was performed under the National Cooperative Highway Research Program (NCHRP) Project 18-08A to develop a statistically based experimental methodology to efficiently determine the optimum mixture proportions of concretes based on locally available materials and performance requirements.
Download
http://s18.alxa.net/s18/srvs2/02/002...idge.Decks.rar